Hot Product
Refractory Knowledge
Causes of reticular cracks in high alumina refractory bricks
Date:2018-06-25 15:32 From:Zhengzhou Sunrise Refractory Author:admin
The appearance of mesh cracks on the surface of high-alumina bricks often presents shortcomings when producing high-alumina bricks, and the reason for the onset of mesh cracks is complicated. Clinker impurity content (especially R2O content), degree of sintering, critical particle size, fines participation, mixed mass of the mud, humidity and temperature of the dried body of the green body, shortening of the body during the firing process, and The secondary mordenization reaction and the recrystallization effect of corundum all cause the appearance of the product to attack the texture. The sintering of high-alumina bricks is liquid phase sintering, and the constituent temperature and liquid phase of the liquid phase, the heating rate during firing, and the atmospheric conditions are also important factors that cause inconsistency and shortening and form external network cracks.
The degree of sintering and the firing atmosphere and the evaporant present in the gas phase have a great influence on the appearance of high-aluminum products. The poorly sintered clinker continues to shorten during the firing process of the product, causing cracking and cracking of the product. In the poorly sintered clinker, the secondary mullitization is insufficient. In the firing process of the product, the clinker itself Sub-Moroli petrochemicals are still continuing. This is an intrinsic factor in the inconsistency of formed products, resulting in an increase in the number of reticular cracks and an increase in the degree of cracking. The degree of mesh cracking of the product's appearance is also closely related to the water absorption of the clinker chosen. The greater the water absorption of the clinker, the greater the degree of cracking of the texture. When using clinker bricks with a high water absorption rate, the clinker itself will continue to complete the sintering process during the firing process, and the products will be shortened and non-uniformly, so that cracks and webs are simply present. Another firing atmosphere in the kiln is also one of the causes of cracks in high-grade aluminum products. When firing high-alumina products, the atmosphere in the kiln needs to be weakly oxidized and the excess air coefficient is controlled to 1.1-1.2. The practice indicates that the appearance of network cracks in the product has the tendency of increasing the excess air coefficient and reducing, but the excess air coefficient should not be excessively shaken.
In addition, cracks in the appearance network of the product mostly occurred in the brick surface within the code brick gap. Therefore, when the excess air coefficient in the kiln is small, or when the atmosphere is restored, because the brick seams are small, the CO simply stays in these areas, so that the Fe2O3 in the product is restored to FeO; the tile facing the channel is relatively smooth in appearance and airflow is relatively smooth. , so will not be affected by changes in the atmosphere, there is no network cracks. Special attention is paid to the fact that frequent changes in the nature of the combustion atmosphere should be prevented during the firing process. Thus the effect of this alternative change will be to damage the appearance.
It can be seen from the chemical analysis of the outer and central parts of the products with more cracks on the outer surface that the Al2O3 of the brick body surface is 1%-2% higher than the center, and the SiO2 is 1%-2% lower, and the NaO is 10 times higher than the center. the above. According to the analysis of the phases, the mullite content in the epidermis is 12% lower than the center, the corundum content is 4%-5% higher, and the glassy phase content is 7%-8% higher. This shows that during the relocation process of Na2O, Na+ evaporates and adsorbs on the outer surface of the high-alumina brick. It will promote the decomposition of mullite, reduce the appearance of mullite, and increase the corundum and glass phases. Because the appearance of the liquid phase increases and advances, the brick surface is prematurely shortened, resulting in the onset of moire.
Practice indicates that in order to prevent and reduce the onset of network cracks, the water absorption rate of 1.2. grade high bauxite clinker is controlled to be below 4%-5% respectively, and the water absorption rate of mill powder should also be controlled below 6%. It is appropriate to control the air coefficient between 1.1-1.2, and it should be adjusted by thermal engineering to keep the firing of high-alumina bricks in a stable weak oxidation atmosphere.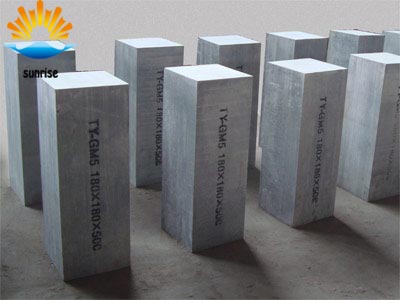
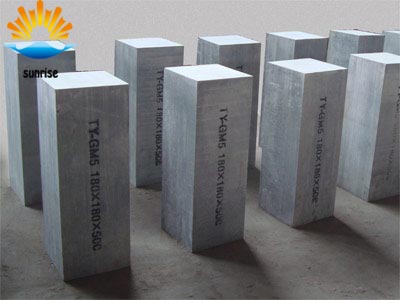
Inquiry:
If you have any questions or good suggestions on our products and site, or if you want to know more information about our products, please write them and send to us, a representative will contact you within one business day. We guarantee that your information will not be divulged to the third party.