Hot Product
Refractory Knowledge
Preparation of High-End Special Magnesia Refractory Products
Date:2016-08-02 00:13 From:Zhengzhou Sunrise Refractory Author:admin
Special refractory materials are a type of high-temperature ceramic materials with special properties and special functions made of a single material or composite materials such as high melting point high-purity oxides, non-oxides and carbon as raw materials by traditional production processes or special production processes developed on the basis of the traditional ceramics and refractories.
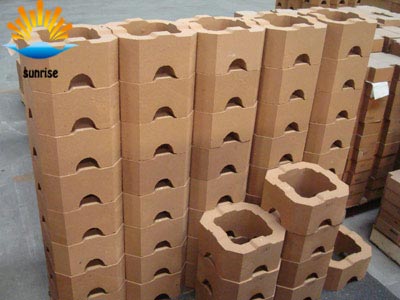
Special refractory materials are always made of high purity raw materials which are synthetic and purified but seldom natural ingredients. Special production processes such as ultrafine technology, spray granulation technology and special molding technology (isostatic molding, thermoforming, injection molding, etc.). They normally requires fine powder, a few microns to tens of microns, by high temperature calcination at 1800+℃, under various atmosphere or vacuum conditions. The general process includes raw material purification treatment, grinding, batching, molding, drying, baking, firing, rough processing and final processing.
Refractory materials include refractory oxide materials and composite materials, high melting point non-oxides (carbides, nitrides, borides, silicides, sulfides, etc.) and composite materials, metal ceramics, high temperature coatings and fiber-reinforced materials.
Because of the special properties of special refractories, they are widely used in science and technology, military, aviation and various high temperature industries in the national economy.
Magnesia is a refractory oxide with a melting point of 2800℃. It belongs to the cubic crystal system, NaCl-type structure, 6 Mohs hardness and a theoretical density of 3.58g/cm3. It has good electrical insulation and high thermal expansion coefficient. Its average thermal expansion coefficient at 20-1000℃ is 13.5×10-6/℃; its thermal conductivity at 100-1000℃ is 6.96W / mk. Magnesia products have a higher vapor pressure and are greatly influenced by atmosphere during use. In an oxidizing atmosphere, they can used at 1700℃. Above 1700 ℃, they will be reduced to metal magnesium. In vacuum, they can be used at 1600-1700℃.
High Purity magnesia is decomposed and purified from magnesium ore. Industrial MgO is mainly produced from magnesite, brucite, dolomite and seawater. First, raw materials are processed through acid and alkali chemical reaction to get a variety of magnesium salts. Then magnesium salts are processed through thermal decomposition, further chemical treatment or heat treatment to obtain high purity magnesia. The heat treatment process includes the removal of physical water and structured water, removing ion through the decomposition reaction, sintering and grain growth. If magnesia with better activity is desired, the calcination temperature should be controlled below 1000℃. Magnesia with different sources, impurities and content will have different sintering properties, calcination temperature and recrystallization properties. Magnesia obtained by the thermal decomposition of brucite has the best sintering properties, the greatest bulk density, while magnesia obtained by the thermal decomposition of bischofite has poor sintering properties.
Depending on the molding method, special magnesia refractory materials can be divided into casting products, extruded products, isostatic molding products, ramming products and machine press products. Casting products mainly include production of crucible, tubular products and sheets. Extruded products mainly include round rod and tube. Isostatic molding products mainly include crucible and insulation materials.
Casting magnesia products
Usually casting magnesia products are made by the slurry casting method. It is more complex than other oxide products, because of the hydration of magnesia. This must be taken into consideration so as not to produce a lot of waste products.
(1) Raw materials
Before production, mix magnesia powder with distilled water into slurry. Then the slurry is hydrated for three days to fully hydrate magnesia to produce magnesium hydroxide. Then it is drained and dried below 100℃. Then it is loaded into a corundum sagger and calcined at 1450-1600 ℃ for 6-8 hours to re-decomposed magnesium hydroxide into magnesia.
(2) Preparation of slurry
Put the re-decomposed magnesia into corundum milling drum and dry ground for 45-90 hours and wet ground by adding water for 75-90 minutes to obtain suspension slurry. Typically hydrochloric acid is added to adjust the PH of slurry to 7-8. Then the slurry is screened through a 100 mesh screen to remove bubbles.
(3) Molding and drying
Pour the slurry into a plaster mold. Then remove the green body from the mold after 1 hour. The green body is dried for 24 hours at 70℃. The dried green body is bisque fired at 1250℃ and processed.
(4) Firing
The green body is sealed into a corundum sagger and fired in 1750-1800℃. Then maintain the temperature for 2 to 4 hours. The bulk density of the finished products can reach up to 3.47-3.54g/cm3.
The process is as the follows:
Raw materials→Fused phase inversion→crushing→magnetic iron removal→distilled water hydration→drying (less than 100 ℃)→calcining (1450-1600 ℃, 8h)→crushing (less than 3.327mm)→Dry fine grinding (45 ~ 90h)→ice water wet milling (75 ~ 90min)→casting→drying (less than 70 ℃)→bisque firing (1250 ℃)→Green body Repair→firing(1750-1780℃)→ finished product.
Isostatic molding magnesia products
Magnesia crucibles are mainly produced by the isostatic molding method. They have better thermal shock resistance than casting products. They are used for the smelting of rare metals, platinum group metals and the purification of their alloys, nickel-based superalloy metallurgy and iron-boron permanent magnet materials smelting. They have achieved satisfactory results.
(1) Raw materials
The chemical composition of high purity fused magnesia includes MgO≥97.5%, SiO2≤0.6%, CaO≥1.2%, Fe2O3≤0.5% and Al2O3 ≤0.20%. its C/S is ≥2, the loss on ignition is ≤0.17% and the bulk density is ≥3.45g/cm3. The main phase of fused magnesia is periclase, a small amount of secondary crystalline phases C2S and no low-temperature silicate glass phase.
(2) Crushing
Selected qualified fused magnesia is crushed by jaw crusher and then crushed into ≤2.5mm aggregate by roll crusher. Iron is removed by a magnetic separator. 1-0.074mm fine aggregate is extracted and fine ground in a rubber lining ball mill with corundum balls as grinding media for 48h. The particles of the fine ground fused magnesia should be ≥90% through a 200 mesh screen.
(3) Mixing
Mix the materials in small mixing sand. The amount is 300Kg each time. The mud should run out on time. The ratio of the ingredients is 40-45% 2.5-0.5mm fused magnesia, 20% ≤0.5mm, 35-40% ≤0.074mm and 2-3% binder.
(4) Molding
Crucible products are molded in a cold isostatic pressing machine. The molding pressure is 150-200MPa. Depending on the crucible capacity, there are Ф200, Ф320 and Ф460 isostatic pressing machines. The mold is coated with a layer of oil-resistant rubber and has a steel core. The rate of contraction of the mold is 25% of the thickness of the finished crucible. The material is loaded from the periphery. When loading, the confluence of the rubber sleeve and the mold core should be fastened with thin steel wire. Load the materials when vibrating on the vibration table. Finally, it is sealed with a rubber sealing cap and fastened with thin steel wire. The material should be uniform and dense.
(5) Drying and firing
After molding, green body is naturally placed for more than 24h, dried at 120℃ for 6h and fired at 1700℃ for 6h. When firing, use high purity 2.0-0.5mm fused magnesia as sand bed.
Inquiry:
If you have any questions or good suggestions on our products and site, or if you want to know more information about our products, please write them and send to us, a representative will contact you within one business day. We guarantee that your information will not be divulged to the third party.