Hot Product
Refractory Knowledge
What is the definition of high density magnesia and product characteristics?
Date:2019-12-19 15:41 From:Zhengzhou Sunrise Refractory Author:admin
As the basic raw material of alkaline refractories, the bulk density of magnesia has an important influence on the use performance of magnesium refractories, especially the resistance to slag erosion and high temperature strength. Studies have shown that refractory materials produced with high-density and high-purity magnesia can significantly increase the service life of metallurgical furnaces. Therefore, improving the quality of magnesia, such as density and purity, has become a focus of research on magnesia raw materials.
The main component of magnesia refractory is MgO, and the main crystal phase is periclase. The periclase is an equiaxed crystal system with a NaCl structure and a lattice energy of up to 3935 kJ / mol, so its melting point is up to 2800C. The lattice constant and true density of periclase decrease and increase with increasing calcination temperature, respectively. The fully sintered periclase has a lattice constant of 0.42nm and a true density of 3.58g / cm '.
However, it is difficult to burn to such a high density due to its high melting point. When making periclase from magnesite, even if the sintering temperature is as high as 2000 "C, the dead burned magnesia is formed, the density does not exceed 3.4g / cm '. Moreover, it is difficult to make products from this raw material. It is difficult to obtain high-density materials for sintering. Therefore, in order to obtain high-density magnesia, the second phase is usually added. From the phase diagram of magnesium oxide, it can be seen that the addition of a single Al2O3, Cr2O3, FeO or FezO3 can make the melting point of magnesium oxide Decreased, but not significantly.
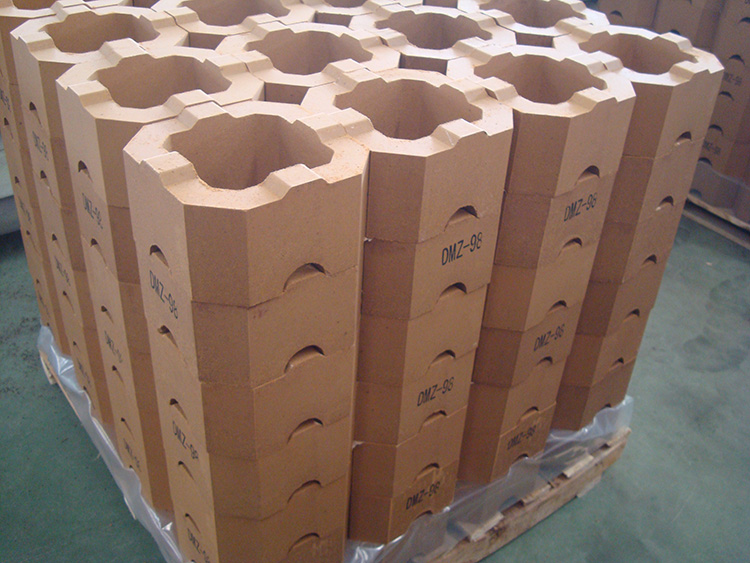
The superiority of high-iron magnesia is mainly reflected in the following three aspects:
①Good sintering performance. Under weak oxidation and reduction conditions, slightly higher than 1300C, high CF (a-fe: O,) dead burned magnesite has appeared liquid phase to promote sintering of the mixture and can produce Excellent ceramic bonding.
② High fire resistance. In many steelmaking processes, the refractory lining is often under a strong reducing atmosphere, which causes C.F to decompose into CaO and magnesite. Through this process, the fusible body is transformed into a solid phase during the erosion of the mixture, and MF is formed by absorbing Fe; O3, thereby forming MW, and the sintered body (magnesia) is enhanced.
③ Strong resistance to slag erosion. During the decomposition of CF, CaO is released and reacts with the infiltrated slag. As a result, the CaO / 5IOQ; ratio and Ca0 / Al: O3 ratio of the infiltrate increase, and the solid phase temperature rises accordingly.
Inquiry:
If you have any questions or good suggestions on our products and site, or if you want to know more information about our products, please write them and send to us, a representative will contact you within one business day. We guarantee that your information will not be divulged to the third party.